There is much interest in this topic from wet-shaving newcomers and veterans alike. In addition, there is just as much vehemont and vociferous opinions one way or the other. This article’s goal is to lay out the differences objectively and give a solid reason for the wildly varying price differences among seemingly similar brands. While this article will not go into specific details about why company A’s brushes cost $350, while company B’s brushes only cost $45, this article will explain to you the factors that go into the pricing of a brush. Factors both tangible and intangible, such as handle material, hair quality, and brand name recognition.
This article is split into the following sections: handles, hair knots, labor costs & quality control, research & design, and “good will.” The article will conclude with a section on where to find the true “hidden gems.”
The Handle
The handle is an often overlooked aspect of a shaving brush. In many cases, the handle design and materials represent the only difference between two brushes. The handle itself can cost more or as much as the knot. There are two ways in which handles are made out of the various materials used: lathe turned or molded. While construction by hand is possible, it is not practical for large scale operations.
Lathe v. Injection Molded
The simple truth is that lathe turned brushes require more labor and much more time. Even if a CNC lathe is used. The more labor used, the more a handle costs, and time is labor. It is simply much faster and easier to make molds and produce many handles in a given timeframe vs. a few if turned by lathe. Human operation of a lathe will also introduce inconsistencies from handle to handle, no matter the skill of the operator. Some of these inconsistencies are thrown out, adding to the cost.
Lathe turned handles are also extremely wasteful as much of the mateirla is discarded as waste. A brush handle starts off as a cylindrical rod. Material is then removed from the cylinder using tools until the desired shape is formed. Not only is this practice more costsly in terms of unused product, but the actual rods cost more per handle than a molded handle of the same exact type of material.
Some materials, and all natural materials known to this author, require a lathe to be used in handle construction because a cylinder or a block is the only form the material comes in. Some handle designs must be molded due to the squared sides. See Thater handles.
From a performance standpoint, there is no advantage to a lathe turned handle vs. a well made molded handle. While lathe turned handles are generally made from better materials, there is nothing preventing molded handles to be made from the same acrylic resin material. That said, there are some limits to the lips & edges a mold can produce reliably. See Simpsons Chubby.
Where lathe turned handles make the most sense is in micro manufacturing of a few dozen pieces. In order for a mold to be efficient, hundreds of handles must be produced. Of course, hundreds of handles means more efficiency and an economy of scale.
Material
Natural and rare material such as horn, exotic woods, and specialty resins impart added cost and rarity to the brush soley due to the rarity and cost of the material used. Common & inexpensive woods are actually cheaper to produce (even on a lathe) than quality molded resin handles. Added features such as a metal base, special acrylics, or special shapes & colors likewise add to the cost. See Baxter’s of California brushes.
While it is entirely possible to use plastic to make a handle, only the cheapest of brushes go this route. See Frank Shaving’s “plactic” version of the Richmond model. A wood handle is nearly the same price and looks and feels of higher quality. Most low cost brushes will go the wooden handle route to cut a few more dollars. However, many mid or low-mid range manufacturers opt instead for resin handles. They are simply better and feel more substantial.
There are two types of basic resins. Regular resin and acrylic-resin. Acrylic resin is harder and slightly denser compared to regular synthetic resin (you would be very hard pressed to make out the difference unless you were specifically told this handle is resin and this handle is acrylic). As such it takes a slightly better polish and scuffs less easily. See the wikipedia page for other benefits. The downside to acrylic resin is that it costs more.
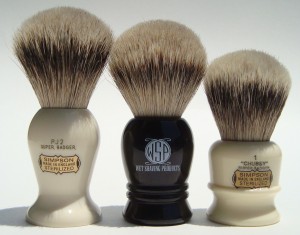
Molded resin handle next to lathe turned acrylic resin handles
A manufacturer may use any combination of the above manufacturing methods and material options, as long as the medium allows it.
The Knot
We now come to the topic which generates the most debate and confusion. The actual knot of hair that makes the shaving brush, a shaving brush. You may be surprised to know that there are actual real and tangible differences between the hair knots used by the top tier v. the low tier brands.
Density
Let’s start with density. When comparing the knot quality amongst the different brands, the hair density is the easiest perceptible difference to measure. Simpson’s Chubby and Shavemac’s D01 are exemplars of the industry’s densest knots. On the other hand, low end silvertip badger hair is usually sparsely populated.
For obvious reasons, adding mroe hair to the knot adds to the cost. Not only does it require more hair, but more labor as well. Hair density is the first area cheap brushes skimp on.
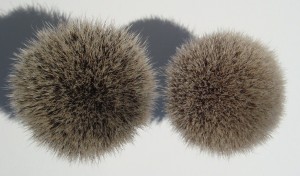
Low Density Frank Shaving brush compared to High Density WSP brush
Hair Grade
Here is where the vociferous debate begins and ends. Hair quality. There is no industry standard of hair grades. The closest standardization across the industry is to group the hairs by type of hair and species of badger. There are only four types of hairs that come from the two species of badger used to make brushes. Each species has a band of white/light colored hair and the rest is black or grey. What follows is a brief description of the major types of hair.
Silvertip hair comes from the Eurasian Badger and consists of the light band of hair seen on the badger around the neck and shoulders. It has a distinct narrow black band towards the tip. The tips are light in color. Within the broad category of silvertip lies different grades of silvertip hair. These grades are based on length of individual hairs and softness. Each brand can invest more time and labor into the process to improve the sorting process and ensure a higher grade of hair or a specific trait they are looking for.
Two band hair actually consists of three bands, the middle band is just really long. The overall hair is also really long. It comes from the same area of the badger, but instead of the Eurasian Badger, it comes from the Hog Badger. The two band appearance comes from adjusting the loft height to hide the bottom white band. Just as with silvertip hair, each brand can cherry pick the longest and softest hairs to make their own grade of hair. See Simpsons Manchurian, M&F Blonde Badger, or Rooney Finest.
All other badger hair is from the darker hair of the animal or is a blend of hairs. Lower hair grades such as “best” may even consist of rejected silvertip or 2 band hair. As you can see, without additional grading and sorting, soft hair can be mixed with rougher hair. Thus, creating a lot of variance within a brand. Some manufacturers artifically enhance badger hair by making the tips whiter and using conditioner in an effort to make the tips softer. They aren’t really softer in this author’s opinion. See The Golden Nib Super Badger knots.
As you may have already concluded, the hair used in high end brusehs may well be of a higher quality due to the additional hand sorting and grading involved. For example, TGN’s silvertip grade A may well be the equivalent of EJ’s silvertip, but it is not as soft as Simpson’s super badger grade.
Whether this small difference justifies some of the extreme price differences is up to you the consumer.
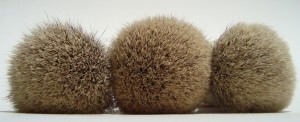
So soft…
Labor Costs, Country of Manufacture, & Quality Control
It is an inescapable fact that some countries have lower labor costs than others. The people living in these countries are no less capable or intelligent. Circumstances and lack of development have simply made things that way.
As such, the more labor performed in higher cost countries, the higehr the price of the finished product. The more English labor involved in the manufacture of a brush, the higher the price to the consumer. It should be noted that foreign countries’ “made in” laws are not as strict as the United States’ laws are. The U.S. requires that all of the significant manufacturing must be done in the US, otherwise it needs to be labelled as assembled in the US. See Bureau of Consumer Protection Guidelines. Not so with other countries. Some countries only require the “final step” to be performed in the country.
Along with labor costs in general is the principal of quality control and quality of labor. The best brush brands generally invest more into quality control and quality of the labor. Such companies will have excellent warranties and little to no issues with their product.
Lower cost brands will typically rush their workers and require them to produce a lot of knots or handles per hour. They operate on an economy of scale, lowest cost mindset. They are more likely to let errors slip by, such as glue in the knot. This does not mean that low wage countries are unable to produce high QC goods. To the contrary, Apple is produced in China, as are many high end luxury goods these days. What matters is what the buyer tells the factory they want and whether they are willing to pay a higher price for more quality control, or do it on their end.
Research & Design
A little talked about, but very important, aspect of brush manufacture is the design of the brushes. Speaking from firsthand experience, there are a lot of different factors that go into a brush. Aside from the obvious choices of handle and hair loft, there are many details most people never realize. Details such as: how to grade the hair, what type of hair to use, how fan or bulb shaped the knot should be. Even loft choice has several aspects to it. It’s not simply just about how deep of a hole you want to drill. A truly custom brush can customize both the knot length and the hole depth, allowing many combinations.
There is a reason all the Chinese brushes are virtually identical copies of each other. Have you ever wondered why the knots remind you a lot like a Kent BK4? Well, the answer is how Chinese factories are set up and run. They aren’t designed to design products, they are designed to make what the buyer tells them to make. They have all come up with this 55-57 mm lofted brush, which is simply the industry standard there. No one has asked them to produce anything different, and if they did, the entrenched producers will tell you to go away unless you put in a 10,000 brush order. Brands such as Frank Shaving and Lijun & 1980 are primarily produced for the domestic & low end market. The domestic market hasn’t even heard of Simpsons, Shavemac, Thater, Muhle, or even Edwin Jagger.
Unlike the European companies, Chinese people cannot afford a Simpsons brush. It is simply out of their price range. It is unreasonable to expect the Chinese to copy a Simpsons brush if there is no demand for it. Most people in China can’t even afford the silvertip brushes offered by the Chinese companies. While I’m told they do use brushes & soap, I surmise that they predominantly use boar brushes.
Without a passion for wet shaving and brushes and a large stable of brushes to help form an opinion, it is impossible to expect someone to design a truly good brush. That is how all the top tier European brands are run. Truly enthusiastic people are behind the most lauded companies. I can assure you, that is not the case in China and probably in many mid level brush makers. They make what they make because it sells and it works. There’s no impetus to innovate. Without the passion and knowledge driving the design element, the status quo of “just enough” is sure to prevail.
Brand Name/Goodwill
Economists call the extra money people are willing to pay for a name brand “goodwill.” A company’s heritage, image, and branding add intangible costs to the product as consumers are willing to pay more for certain name brands. There is no way around this. With large marketing costs, come higher prices. In addition, people are simply willing to pay more for limited quantities of brand X. In many cases, a significant portion of the brush’s price is simply the markup from a certain brand name. Take Plisson for example.
Where are the Real Deals?
This is the part where I tell you the secret Chinese manufacturers who make extremely good products at rock bottom prices. Well, the old adage, “you get what you pay for” is extremely on point. There are no secret Chinese manufacturers at rock bottom prices. They still need to pay their workers a decent wage and material costs are the same across countries.
The established brands with large marketing expenses will never give you the best value to price ratio because they have a large overhead to meet. However, luxury products are not about compromising.
Given what we have already discussed, the only true “hidden gems” are going to the brushes made in lower cost countries, sold by a startup company taking a loss or less profit to establish a foothold in the market. The other alternative for good savings is to find a company with a very large economy of scale who passes on the savings to the consumer. This author doesn’t know of any such company as brushes are a niche market and involve a lot of manual labor. Only the handles can be truly mass produced by machine.